Medical Industry Experience
Medical Device Manufacturing
Alan McLeod PhD
Alan McLeod PhD, Founder and Director of Health Innovation Support has twenty-five years of experience in the medical industry.
- Secondment to Innovation Hub to provide continuity of innovation support following restructuring of SW AHSN
- First 8 innovations either launched, licensed or at Heads of Terms
Role: Innovation and IP Manager
- Developed an Innovation Pathway comprising Innovation Lead and
- Support Group now adopted at all South West Acute Trusts
- Created foundation for Innovation by putting in place Regional Agreements on non-disclosure, revenue share between Trusts and innovators, ownership of IP and an IP Assignment Package
- Assisted with the evaluation of 105 NHS innovations
- Provided direct support for 38 NHS innovations ranging from concept prototyping, obtaining Regional feedback, licensee identification and licensee relationship management
Role: Business Development Manager
- Support for NHS innovations including innovation generation, evaluation, IP protection, prototype development and licensing
- Project Manager for a Trust’s meniscus stabilisation innovation Contract negotiation on behalf of NHS Trusts
Role: Director and Consultant
- Regulatory Consultant for Concept Spine Ltd
- Management of final setting up Post Market Surveillance Study for
- NuVasive Inc until termination of study in 2010
- Consultancy regarding business development opportunities for non- spinal embroidered implants such as a Rotator Cuff device
Role: Director, Development, Embroidery Technology
- Managed setting up a Post Market Surveillance study of the NeoDisc in the UK
- Managed data analysis from the NeoDisc IDE study linking clinical and radiological results with patient selection and surgical technique
- Managed development of an embroidered artificial disc for the lumbar spine from concept to CE marked device.
- Key player in sale of NeoDisc for $12 million plus $31.5 million in milestone payments to NuVasive Inc. Developed and delivered 45 minute presentation given to over twenty prospective purchasers.
- Responsible for NeoDisc marketing from concept to running the exhibition booth at the 2005 Spine Arthroplasty Meeting.
- Key team member and co-inventor of an endovascular stent-graft. Facilitated subsequent licensing of what is now the AorFix device.
- Worked with Great Ormond Street physician to develop his concept of line locking device, now successfully marketed by Braidlock Ltd.
- Co-inventor and Project Manager for the NeoDisc artificial cervical disc with responsibility from the initial prototype design to fatigue testing and early clinical use as part of a Clinical Investigation approved by the UK regulatory authority.
- Developed rotator cuff device from a surgeon’s initial concept to a CE marked device in successful clinical use.
- Managed activities of Suture Development making key contributions to new value-added suture constructs such as spliced loops and a bi-coloured suture.
- Managed Quality Control Department
- Responsible for approval to Annex II of the Medical Devices Directive allowing Pearsalls to CE mark its own medical devices.
- Developed Quality system first to EN 46001and then to ISO 13485
Role: Technical Manager 1995 - 1997
Worked from within Marketing Department to provided UK-wide, in-theatre technical support for Sofamor Danek spinal systems
Developed SurgiLig acromio-clavicular ligament and a system for stabilising fractured fingers from working with surgeons to establish business cases to CE marked device
Role: Research Manager 1992 - 1994
Project Manager for the Horseshoe intervertebral fusion system
Role: Research Fellow 1989 - 1992
Developed system of mode of failure analysis that lead directly to elimination of early failures of the ABC artificial ligament.
Role: Research Assistant 1984 - 1986
Designed and manufactured first ABC artificial knee ligament. Wrote manufacturing procedure and trained first production staff
Alan designed a braided artificial anterior cruciate ligament which is one of the main structural supports in the knee. He manufactured the first device, wrote the production documentation, trained the production staff and trained the quality control staff. Thousands of these ABC ligaments were implanted. Alan’s PhD established why an artificial knee ligament was breaking in clinical use.
A number of the Surgicraft ABC artificial knee ligaments were failing in clinical use with some ruptures occuring spontaneously within a few months of implantation.
The broken ligaments were sent back to Alan for mode of failure analysis in order to establish why they were breaking. The clinical hypothesis was that the ligament was just not strong enough and needed to be strengthened.
Alan was a post-graduate student at the Department of Textile at UMIST (now part of the University of Manchester) where there was experience in the study of why textiles such as mooring ropes failed.
Alan cleaned the tissue off the explanted ligament using enzymes in an incubator in order to expose the polyester filaments at the failure point so that the fracture morphology could be examined using a scanning electron microscope.
Alan was able to establish that the ABC ligaments were failing at the point where they emerged from the tibial drill hole into the knee joint.
Any failure of the ABC ligament within the first year of implantation was associated with crushing and flattening of the polyester over a matter of just a few millimetres just level with the edge of the drill hole with just a very few strands failing with tensile breaks.
By working closely with a clinical research fellow, Alan was able to link this crushing and flattening damage to a drill hole that was too far forward in the knee. This placement resulted in the guillotining of the ligament between the intercondylar notch and the edge of the drill hole crushing the polyester and causing sequential failure across the ligament until the last few strands failed with a tensile break.
The route of the ABC ligament used to reconstruct an Anterior Cruciate Ligament in the knee.
The tibial remnant of an ABC ligament that failed in clinical use just at the point where it emerged from the tibia into the centre of the knee joint. Crushing and flattening damage worked its way through the ligament until the last strands on the right failed with tensile breaks.
Crushing and flattening of polyester filaments.
Tensile break of polyester filament.
The establishment of the cause of the failures immediately led to the development of an instrument called a rhino horn to ensure that the drill hole through the tibial was placed just far enough back in the joint to avoid the risk of the ligament being guillotined when the knee was extended and the leg straightened.
The improvement in understanding about the crucial nature of the drill hole position combined with new instrumentation to position and smooth the edges of the drill hole resulted in the elimination of early failures of the ABC Ligament.
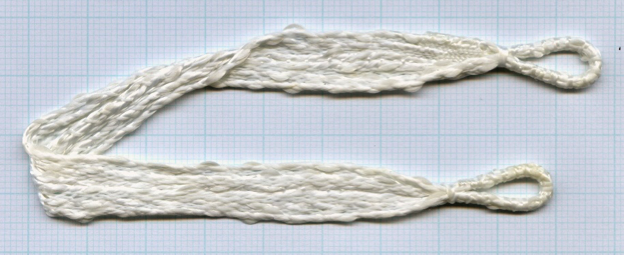
SurgiLig Acromio-Clavicular Ligament
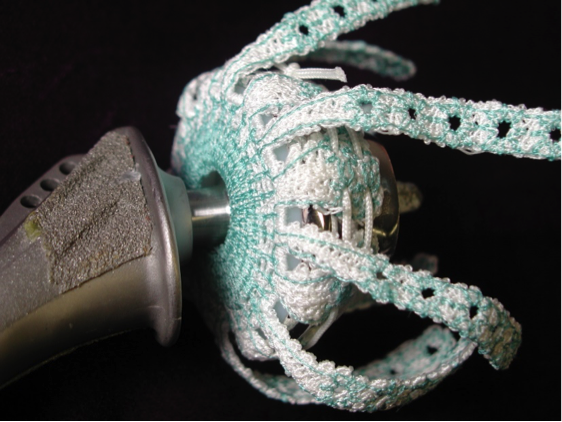
Shoulder Stabilisation Device