Medical Devices Experience
Alan McLeod's Shoulder implant was used to advertise performance textile collection at the Cooper Hewitt Smithsonian Design Museum on 5th Avenue, New York
Alan McLeod PhD
Alan McLeod PhD, Founder and Director of Health Innovation Support has many years of experience in developing innovations for the health sector. Take a look at a sample of innovations of medical devices below.
Intervertebral discs are the shock absorbers between the vertebrae of the spine. If a disc fails, it can press against the spinal cord and must be removed.
Treatment used to replace the disc with material that fused the vertebrae, but this put extra strain on the motion segments above and below the treated level. The NeoDisc was a revolutionary artificial disc design for the cervical spine that perfectly replicated the natural motion of the intervertebral disc.
Alan was the co-inventor and bioengineer behind a revolutionary design of motion preserving artificial disc called the NeoDisc that was developed in Taunton before being sold to the US spine company NuVasive.
The NeoDisc is an artificial disc for the cervical spine, comprised of a silicone core held in place by a jacket manufactured from polyester suture material using computer controlled embroidery.
NeoDisc mounted on artificial neck bones showing the fixation with bone screws.
Cross-sectional view showing the silicone core held in place by a polyester jacket that was manufactured from polyester suture using computer controlled embroidery.
During manufacturing, the silicone core is placed inside the polyester jacket and the fixation flanges are then crossed over or interdigitated. This design feature ensures that the load being transmitted to the silicone core is always a compression load irrespective of whether the neck is being flexed or extended.
Polyester was selected for the jacket because it encourages tissue ingrowth. Comparing the cross-sectional views above, the dark purple on the right is the polyester while the lighter blue/purple is tissue ingrowth.
The surgical technique is shown above. The failed intervertebral disc is removed via the front of the spine. The NeoDisc was designed to conform to the patient so there was a wide range of sizes and a set of sizing trials to select the optimum width, depth and height of device. The selected device was inserted using forceps. The initial mechanical fixation was achieved using bone screws with the long term fixation being provided by the tissue ingrowth.
The polyester does not show up on X-rays but the images above show the first ever implantation of a NeoDisc before and after the surgery.
The MRI scans shown above are of the first patient before and after surgery. The need for the surgery can be seen by the way that the natural disc was pressing onto the spinal cord.
The MRI scan above was taken two years post-surgery and the spinal cord remains uncompressed and the patient was pain free.
The NeoDisc was designed to preserve the natural motion of the spine and three years post-operatively, the first patient retains a full range of motion at the operative level.
Alan designed a braided artificial anterior cruciate ligament which is one of the main structural supports in the knee.
Design:
The ABC ligament was manufactured using a braiding machine using either polyester and carbon fibre or just polyester fibres. Alan manufactured the first device, wrote the production documentation, and trained the production and quality control staff. Thousands of these ABC ligaments were implanted.
The two types of ABC Ligament (see picture above)
Scaffolding Prosthetic
The ABC ligament was designed to provide an immediate prosthetic replacement for an anterior cruciate ligament and then to act as a scaffold for tissue ingrowth.
Appearance of ABC ligament just five weeks after implantation with a new covering of tissue over the ligament within the knee joint.
The tissue was not just a surface covering. Shown above is a cross-sectional view of an ABC Ligament which failed in a re-trauma after 26 months. The tissue has penetrated right through the device.
This tissue ingrowth was also seen into the all- polyester ABC ligament. Shown above is a cross-section through a ligament that was ruptured after 32 months.
The tissue ingrowth was not just random scar tissue. Shown above is an image from a Scanning Electron Microscope taken by Alan showing collagen fibres orientated along a single 0.02mm diameter filament of polyester from an ABC ligament that failed in a re-trauma after 27 months.
Abdominal aortic aneurysms are caused by the wall of the aorta ballooning out of shape. The preferred way to treat these is to create a new lining through the middle of the weakened section using a stent-graft which is inserted via a catheter and opens out when in situ. Alan was part of a team that developed a stent-graft using computer controlled embroidery to stitch a memory metal stent onto a polyester base fabric.
The sides of the flat embroidery are then stitched together to form the tubular stent graft. Alan was responsible for developing and then training the production staff to hand-stitch the seam that must be blood-tight and structurally sound.
The rotator cuff is the soft tissue that stabilises your shoulder joint. Tears of the rotator cuff become more common with advancing age and large tears can be very debilitating.
Alan's rotator cuff device was manufactured from polyester suture using computer controlled embroidery. The design uses a series of chain-linked fixation holes which provide secure fixation points.
The unused material can simply be cut off without weakening the strength of the remaining implant.
Alan’s PhD established why an artificial knee ligament was breaking in clinical use.
A number of the Surgicraft ABC artificial knee ligaments were failing in clinical use with some ruptures occuring spontaneously within a few months of implantation.
The broken ligaments were sent back to Alan for mode of failure analysis in order to establish why they were breaking. The clinical hypothesis was that the ligament was just not strong enough and needed to be strengthened.
Alan was a post-graduate student at the Department of Textile at UMIST (now part of the University of Manchester) where there was experience in the study of why textiles such as mooring ropes failed.
Alan cleaned the tissue off the explanted ligament using enzymes in an incubator in order to expose the polyester filaments at the failure point so that the fracture morphology could be examined using a scanning electron microscope.
Alan was able to establish that the ABC ligaments were failing at the point where they emerged from the tibial drill hole into the knee joint.
Any failure of the ABC ligament within the first year of implantation was associated with crushing and flattening of the polyester over a matter of just a few millimetres just level with the edge of the drill hole with just a very few strands failing with tensile breaks.
By working closely with a clinical research fellow, Alan was able to link this crushing and flattening damage to a drill hole that was too far forward in the knee. This placement resulted in the guillotining of the ligament between the intercondylar notch and the edge of the drill hole crushing the polyester and causing sequential failure across the ligament until the last few strands failed with a tensile break.
The route of the ABC ligament used to reconstruct an Anterior Cruciate Ligament in the knee.
The tibial remnant of an ABC ligament that failed in clinical use just at the point where it emerged from the tibia into the centre of the knee joint. Crushing and flattening damage worked its way through the ligament until the last strands on the right failed with tensile breaks.
Crushing and flattening of polyester filaments.
Tensile break of polyester filament.
Establishing the cause of the failures immediately led to the development of an instrument called a rhino horn, which ensured that the drill hole through the tibial was placed just far enough back in the joint to avoid the risk of the ligament being guillotined when the knee was extended and the leg straightened.
The improvement in understanding about the crucial nature of the drill hole position, combined with new instrumentation to position and smooth the edges of the drill hole, resulted in the elimination of early failures of the ABC Ligament.
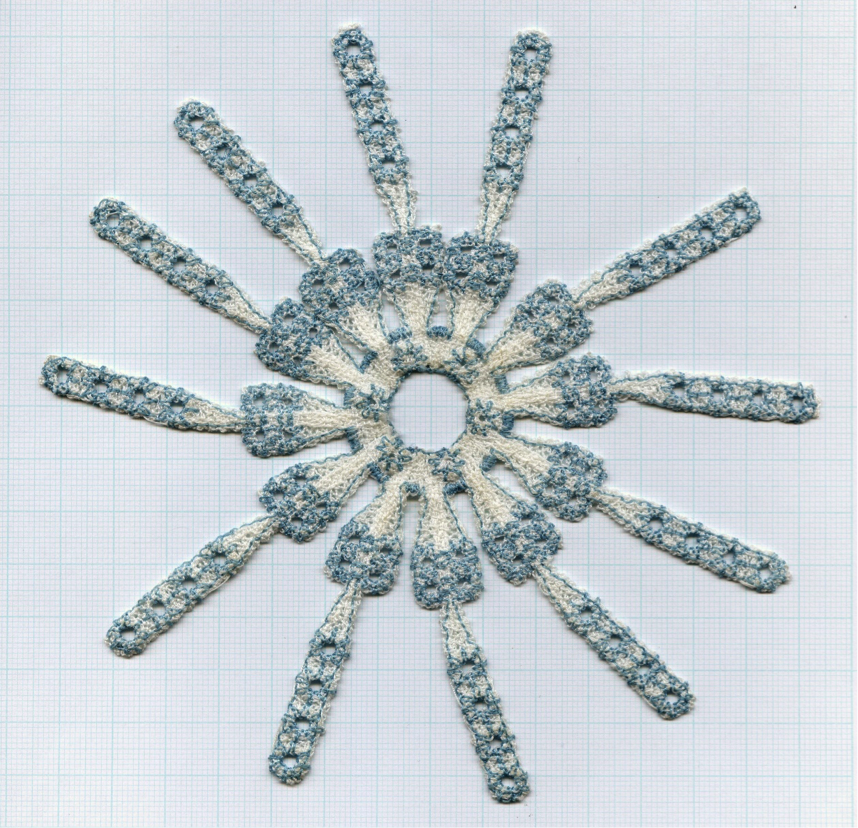